Welcome to Your Guide to Battery Laser Welding: Getting Started and Succeeding! Whether you’re a novice or an experienced professional, this guide is designed to help you become familiar with the basics of battery laser welding. Inside, we cover everything from safety protocols and materials selection to specialized techniques that will enable you to achieve superior results.
With our step-by-step approach, you can master the fundamental principles of this powerful technology and take your work projects—and career—to the next level. So let’s get started on your journey towards becoming a successful battery laser welder!
Introduction to Battery Laser Welding
Battery laser welding is one of the most widely used techniques in manufacturing today. Its an efficient and reliable way to join two pieces of metal or other materials together, without compromising on quality or accuracy.
This guide will provide an introduction to battery laser welding, outlining its benefits and applications, as well as providing expert advice for getting started successfully. At the heart of every battery laser welding process lies a powerful yet precise beam of light – generated by either a CO2 or Nd: YAG (neodymium-doped yttrium aluminum garnet) type laser source – that melts metal at extremely high temperatures with pinpoint accuracy. With this technique, it’s possible to weld virtually any joint configuration including butt joints, lap joints, and T-joints quickly and accurately with minimal heat-affected zone (HAZ).
However, there are certain prerequisites for successful battery laser welding; such as correctly selecting the right power output settings according to material thicknesses; choosing appropriate filler rods; using compatible shielding gases; maintaining proper contact pressure between components, etc., all of which can be daunting tasks.
To ensure success from your first attempt you must understand these principles thoroughly before starting. With this knowledge in hand let’s look at some key considerations when implementing a battery laser welding application: Firstly, the selection of suitable equipment is critical – those equipped with modern advanced features like closed-loop control systems that allow for enhanced precision should be favored over generic models due to their improved capability in performing complex jobs accurately with less operator input required while also reducing setup time substantially.
Secondly, selecting the right combination of parameters such as beam diameter size/shape, pulse duration/shape, etc., is equally important since different metals have varying melting points requiring specific temperature profiles during the fusion process.
Lastly, robust post-processing strategies must always be employed after each weld cycle for final inspection before delivery. In conclusion, Battery Laser Welding provides excellent performance advantages over traditional methods when implemented properly but requires careful consideration if maximum results are desired from the start-up.
With so many variables involved it pays dividends to take time to familiarize yourself with this technology before attempting production runs allowing you to make the best use of available resources achieving the highest levels of productivity reliably and safely!
Key Benefits of Battery Laser Welding
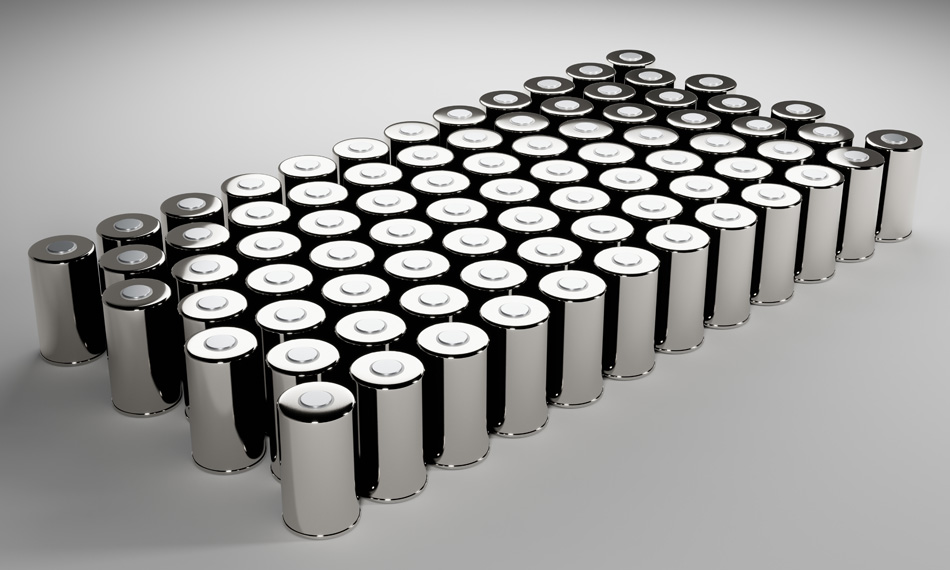
Battery laser welding offers a variety of benefits to users, making it an ideal choice for many different applications. For starters, the process is faster and more precise than traditional welding methods because lasers weld with pinpoint accuracy and heat up quickly.
This makes battery laser welding perfect for high-volume production projects that require precision and speed. Additionally, since battery laser welding does not involve contact between two pieces of metal or other materials, there is less risk of contamination or corrosion damage that can occur in other types of welding processes.
Finally, battery laser welds also create high-quality seals without leaving any visible marks on the material being joined together; this ensures a clean finish that looks professional after completion. With all these advantages combined, it’s easy to see why businesses are turning to battery laser welding as their go-to solution for joining materials together.
Necessary Equipment and Supplies for Battery Laser Welding
Battery laser welding requires a few essential pieces of equipment and supplies to get started. First, you’ll need a powerful laser source.
This will provide the heat needed to join your battery components together. Second, you’ll need an adjustable delivery system for directing the beam at your workpiece in a controlled manner.
Third, you’ll need some safety gear like welding goggles or face shields to protect yourself from the bright light emitted by the laser source as well as any debris created by the welding process. Fourth, it’s important to have various sizes of wire mesh on hand that can be used when joining battery cells together with spot welds; this helps maintain the uniform current flow throughout each cell and prevent shorts between cells during use.
Finally, it’s also wise to have several different types of flux available for cleaning off oxidation before beginning each new weld job – this will ensure better quality results while using less power overall!
Tips for Successful Battery Laser Welding Projects
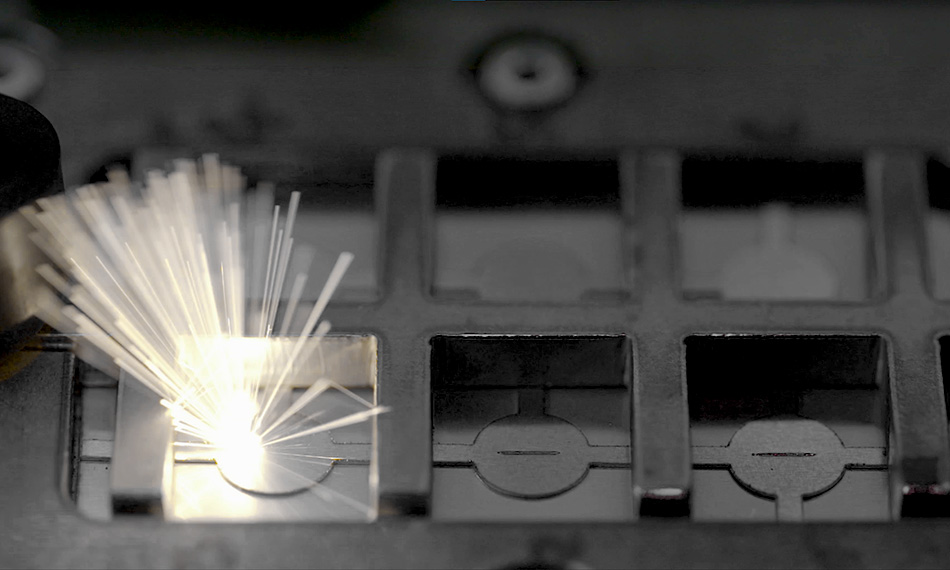
1. Plan Ahead: Before beginning your laser welding project, it is important to plan and determine what type of battery you will be working with, the power source for the welding process, as well as any safety gear or other supplies that may be necessary.
2. Choose Your Laser Type Wisely: There are several different types of lasers available for battery laser welding projects.
The right choice will depend on the size and complexity of your project, so make sure to do some research before selecting a laser type. 3.
Practice First: Even if you have experience in other types of welding projects, try practicing with scrap batteries before attempting a full-scale production weld on an actual product. This can help ensure success and reduce costly mistakes down the line.
4. Develop A Routine Maintenance Program: To keep your equipment running properly, develop a routine maintenance program that includes regular inspections and cleaning procedures according to manufacturer guidelines or industry standards — this will help prevent unexpected breakdowns during production runs that could lead to costly delays or repairs later on down the road.
5. Invest In Quality Materials & Supplies: When it comes to successful battery laser welding projects investing in quality materials and supplies is key — taking shortcuts here could result in lower-quality welds that won’t meet customer expectations or regulatory requirements.
Conclusion
Battery laser welding is a powerful and reliable technology that enables manufacturers to produce complex parts with incredible precision and speed. With the right tools, training, and support, you can get started quickly on your journey of successful battery laser welding projects.
As long as you have access to the right information and resources, it’s easy to understand how this technique works best for your manufacturing needs—and ensure success every time. Battery laser welding offers many advantages over other welding processes, so make sure to take advantage of its capabilities today!