Electrical insulation materials are a crucial part of many industries, from automotive and aerospace engineering to electrical and electronic design. They provide safety, reliability, and durability in the operation of electrical circuits and systems.
In this article, we will explore the science behind these materials, their properties, and characteristics, as well as their applications in various fields. Well also discuss how understanding these basics can help engineers design better solutions for any application they may be working on.
With an ever-increasing demand for efficient operations at lower costs, engineers must understand the fundamentals of insulation material selection so that optimal performance can be achieved with minimal effort.
Overview of Electrical Insulation Materials
Electrical insulation materials are an important aspect of electrical engineering. They offer a range of properties to protect and insulate electrical components from the environment, as well as from one another.
This overview provides information on common types of insulation materials including mica, rubber, Teflon, and polyvinyl chloride (PVC). It examines their characteristics while discussing the advantages and drawbacks of each type.
The article also looks at how these materials can be used in different applications such as power distribution systems and electric motors. Finally, it explores potential improvements that could be made with regard to safety standards when using electrical insulation materials.
Types of Electrical Insulation Materials
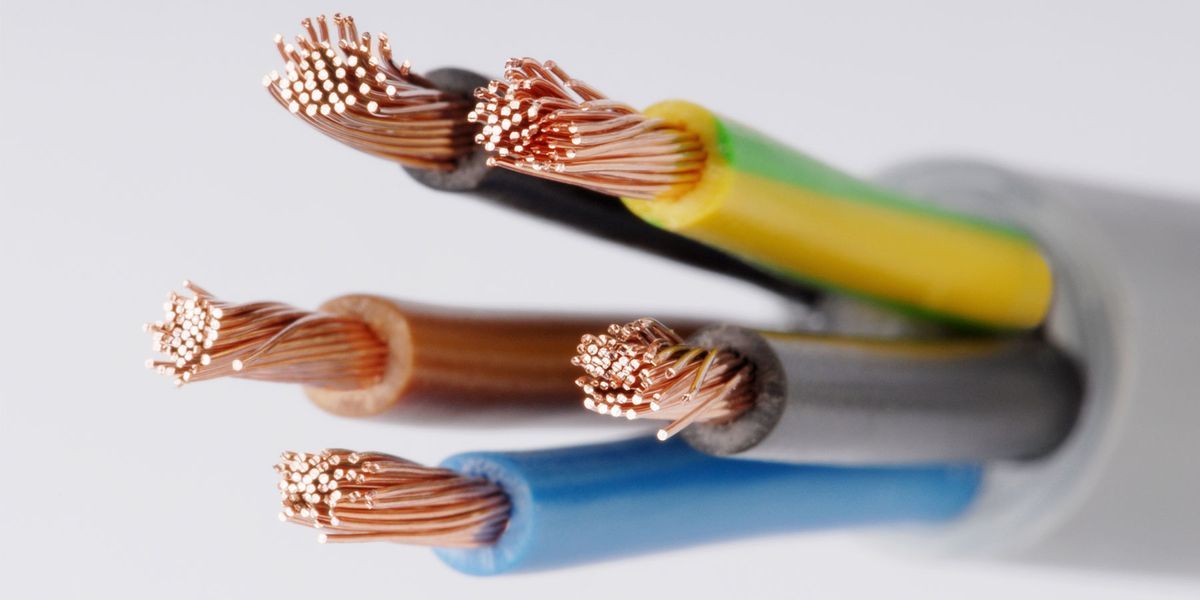
When it comes to electrical insulation materials, there are a variety of types that can be used. The most common include mica, fiberglass, rubber-based insulating materials like neoprene or silicone, and polyethylene foam.
Mica is very strong and durable, making it ideal for high-voltage applications. Fiberglass is also a popular choice due to its fireproof nature and affordability; however, its use in insulation requires frequent maintenance since the material can degrade over time with exposure to heat or moisture.
Rubber-based insulating materials such as neoprene or silicone are often chosen for their superior abrasion resistance compared to other materials but may require additional protection against UV radiation if exposed directly to sunlight. Polyethylene foam tends to be the least expensive option among these types of insulation but offers limited durability in comparison.
In terms of thermal performance, each type has unique characteristics which must be considered when selecting an appropriate material for any given application.
Properties and Characteristics of Electrical Insulation Materials
Electrical insulation materials are essential components in the construction of power and electrical systems. Their properties and characteristics play a major role in determining the safety, longevity, performance, cost-effectiveness, and reliability of these systems.
Electrical insulation materials are designed to prevent current leakage or short circuit between electric conductors or components which can cause damage to people and property. The most common properties of electrical insulation materials include dielectric strength, breakdown voltage, volume resistivity (or surface resistivity), thermal stability/conductance coefficient, flammability rating, and water absorption rate.
Dielectric strength is an important measure used to evaluate the ability of a material to withstand high voltage without breaking down. Breakdown voltage measures how much energy must be applied before breakdown occurs while volume resistivity indicates that material’s resistance against electricity flow through it at any given temperature or frequency.
Thermal stability/conductance coefficient is another important parameter used for evaluating the heat generated by certain types of insulation when exposed to different temperatures over time whereas flammability rating shows how easily a material catches fire under extreme conditions. Lastly, the water absorption rate gives insights into how well a particular material resists moisture from entering its structure over time as this could lead to deterioration in its overall condition if left unchecked for too long periods.
In addition to all these physical properties associated with electrically insulating materials, several other factors such as composition type (organic or non-organic), manufacturing process efficiency (dipping vs casting), and environmental impact should be taken into consideration before making any decisions on their use within specific applications. Its also essential for designers & installers alike to understand what each type offers so they can make informed decisions about which one best suits their needs based on the environment, application requirements & budget constraints they may have available at hand
Applications of Electrical Insulation Materials
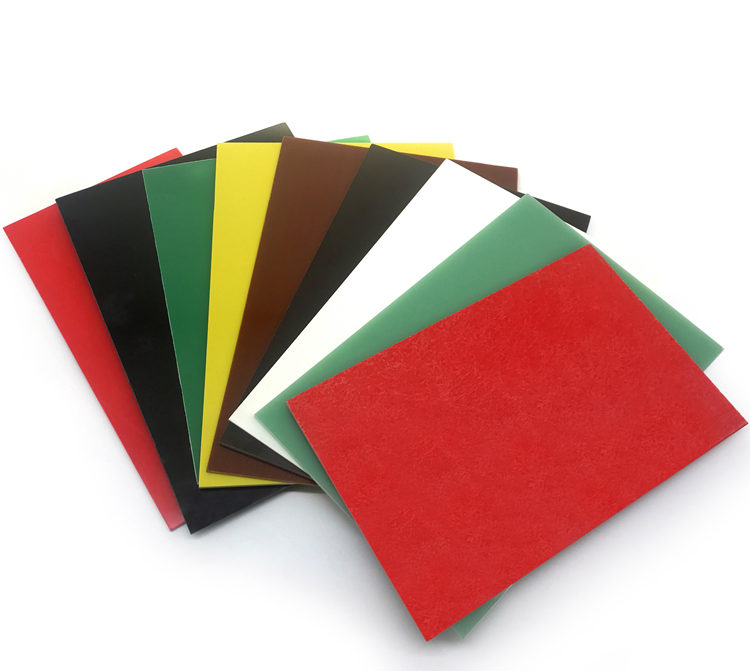
Electrical insulation materials have a wide range of applications in the modern world. From providing electrical protection to preventing short circuits, they are essential components used in many industries for safety purposes.
In the automotive sector, these materials are widely used in vehicle wiring and for the insulation of airbag systems and other electronic components. Electrical insulation materials also find uses in aerospace engineering where they can be utilized as insulators on heat shields or to provide fire resistance to wires within aircraft.
In addition, they are found extensively in high-voltage power transmission lines due to their ability to withstand extreme temperatures and pressures while still providing an efficient path for electricity flow with minimal losses from energy leakage. Furthermore, electrical insulation materials can be applied across various sectors such as medical devices, telecommunications networks, and robotics where their ability to protect against electromagnetic interference is critical for the functioning of the device or system at hand.
Advantages and Disadvantages of Different Types of Electrical Insulation Material
Electrical insulation materials have become increasingly important in modern technology, with various types of insulation offering different advantages and disadvantages. The most popular type of electrical insulation material is rubber, which is often used for cables, wires, and other components.
Rubber offers excellent flexibility and durability as well as being relatively inexpensive to produce. However, it can be prone to disintegrating over time due to UV exposure or other environmental factors. Polyvinyl chloride (PVC) is another common type of electrical insulation material that has a high resistance to fire and chemicals but can be more expensive than rubber-based options.
Additionally, PVC tends to deteriorate more quickly when exposed to sunlight or extreme temperatures compared to some other materials such as fiberglass or polyester film. Fiberglass offers superior strength and heat resistance but it may not provide the same level of flexibility that rubber does; additionally, it’s also heavier than many alternative insulations making it less suitable for certain applications where weight needs to be kept low.
Finally, the polyester film provides good electrical protection while still allowing for flexibility like rubber – however, its cost per square foot may make this option prohibitively expensive in some cases. Therefore careful consideration must be taken into account before deciding on an appropriate form of electrical insulation material based upon the specific application requirements at hand in order to ensure maximum performance whilst adhering closely enough within the budget allocated
Conclusion

Electrical insulation materials are important components in any electrical system. They provide the necessary protection from electric shock, fire, and other hazardous conditions.
These materials have unique properties that make them ideal for use in electrical systems. Their thermal, mechanical, and dielectric characteristics all play a part in determining their effectiveness as insulation materials.
With careful selection and proper installation of the right material, users can ensure the safe and reliable operation of their electrical system for years to come.