When it comes to producing reliable products, environmental test chambers are a key component. These chambers provide an accurate and precise testing environment for products. They help to ensure that all product components can withstand the rigors of their intended use, from extreme temperatures and humidity levels to other environmental factors.
With these chambers, manufacturers can be confident that their products will perform as expected when deployed in challenging environments. Environmental test chambers also allow manufacturers to gain insights into how their products respond to various conditions, allowing them to make any necessary tweaks before release. In short, they are an essential tool for ensuring quality control and customer satisfaction throughout the manufacturing process.
The Different Types of Environmental Test Chambers
Environmental test chambers are essential for ensuring product reliability and effective performance. They come in all shapes, sizes, and materials to meet the testing needs of a wide range of industries. From small temperature-controlled enclosures to large walk-in rooms designed for extreme environmental conditions, these chambers can simulate nearly any type of climate. Here are some examples of the different types of environmental test chambers:
- Temperature Chambers – These chambers allow users to precisely control temperatures ranging from -70°C (-94°F) up to +180°C (356°F). This makes them ideal for testing items that need high or low-temperature stability such as medical equipment, electronics components, automotive parts, and more.
- Humidity Chambers – Humidity is an important factor when it comes to product reliability, especially with electronic devices as they are sensitive to moisture levels. Humidity test chambers simulate real-world conditions by controlling humidity levels inside the chamber anywhere from 10%RH up to 98%RH depending on what is being tested.
- Altitude/Vacuum Test Chambers – Altitude/vacuum test chambers enable engineers and researchers to accurately recreate environments similar to those found at higher altitudes or near space levels where atmospheric pressure is lower than sea level pressure. Simulating these reduced air pressures inside the chamber allows products such as aerospace components or aircraft engines to be tested under realistic conditions before use in actual flight operations increasing safety while reducing risk significantly.
- Rain/Water Spray Testing Chamber – Rain and water spray testing have become increasingly popular among industries due to its ability to replicate natural weathering phenomena which helps manufacturers ensure their products will remain durable even after exposure to outdoor elements over time like rainwater infiltration or ice build-up during winter months. These types’s-test chambers can also be used when evaluating coatings applied on exterior surfaces like paint finishes automobiles boats etc.
- Sand & Dust Testing Chamber– Dust particles can cause damage to electrical components over time leading to premature failure if not properly protected against dust ingress. Sand & dust testing chambers simulate dirt build through the controlled distribution of fine particulates within the environment allowing engineers to evaluate how well products work under harsh dusty conditions. From precision temperature control units down to sand & dust simulation, there are many different types of environmental test chambers available today each designed to tackle a specific set of challenges faced by manufacturers across the globe
Factors to Consider When Selecting an Environmental Test Chamber

When selecting an environmental test chamber, there are a few key factors to consider. Firstly, it is important to determine whether the product you are testing requires hot or cold temperature conditions. This will largely depend on what type of industry your product is intended for and how much stress it needs to endure in its environment. Additionally, you should also assess the size and shape of your product as this could influence which model would be best suited for your needs.
Furthermore, you must take into account the materials used in construction; certain chambers may not be suitable for more delicate parts due to their strength and durability requirements. Finally, the cost must also factor into the decision-making process when choosing an environmental test chamber – cheaper models may have fewer features than pricier ones but they can still provide quality results if appropriate research has been conducted beforehand.
All these considerations should be taken seriously before investing in any type of environmental test chamber so that its potential benefits can truly be realized by ensuring the long-term reliability of products tested within them
Testing Protocols and Procedures for Optimal Performance
Testing products for reliability is an essential part of product development and can be done in a variety of ways. Environmental test chambers are often used to simulate real-world conditions and assess the performance, durability, and safety of products across different temperatures or atmospheres. To ensure optimal results when testing products in environmental test chambers, it is important to have clear protocols and procedures in place that cover every aspect from preparation to final evaluation.
To begin with, all components should be thoroughly inspected before being placed inside a chamber. This includes ensuring that they match any specifications set out by the manufacturer as well as checking for flaws or damage caused by shipping or handling. It’s also important to consider how long each component will be exposed to extreme environments within the chamber; too short an exposure period may not produce meaningful results while too long could cause irreparable harm. Next up is programming the parameters for each product – such as temperature range, humidity levels, and pressure settings – which must reflect those found in its intended environment(s). Parameters should then be monitored throughout testing using sensors located within the chamber itself so adjustments can be made if necessary during use.
Additionally, certain tests may require human input via remote control systems installed outside of the chamber to observe behavior more closely over time – this means having trained personnel available at all times who understand exactly what data needs gathering during these sessions. Finally but most importantly comes assessing whether components have met their expected performance goals based on environmental data gathered from inside the test chamber throughout its operation period; this assessment should include analysis of any physical changes observed over time along with electronic measurements taken periodically (e.g., voltage readings) compared against pre-set standards laid down before the commencement of testing runs.
If all criteria are not fulfilled then a further investigation into why particular elements failed might need to be carried out before retesting can take place again under revised parameters until successful outcomes are achieved as required by industry regulations/standards applicable at that time.
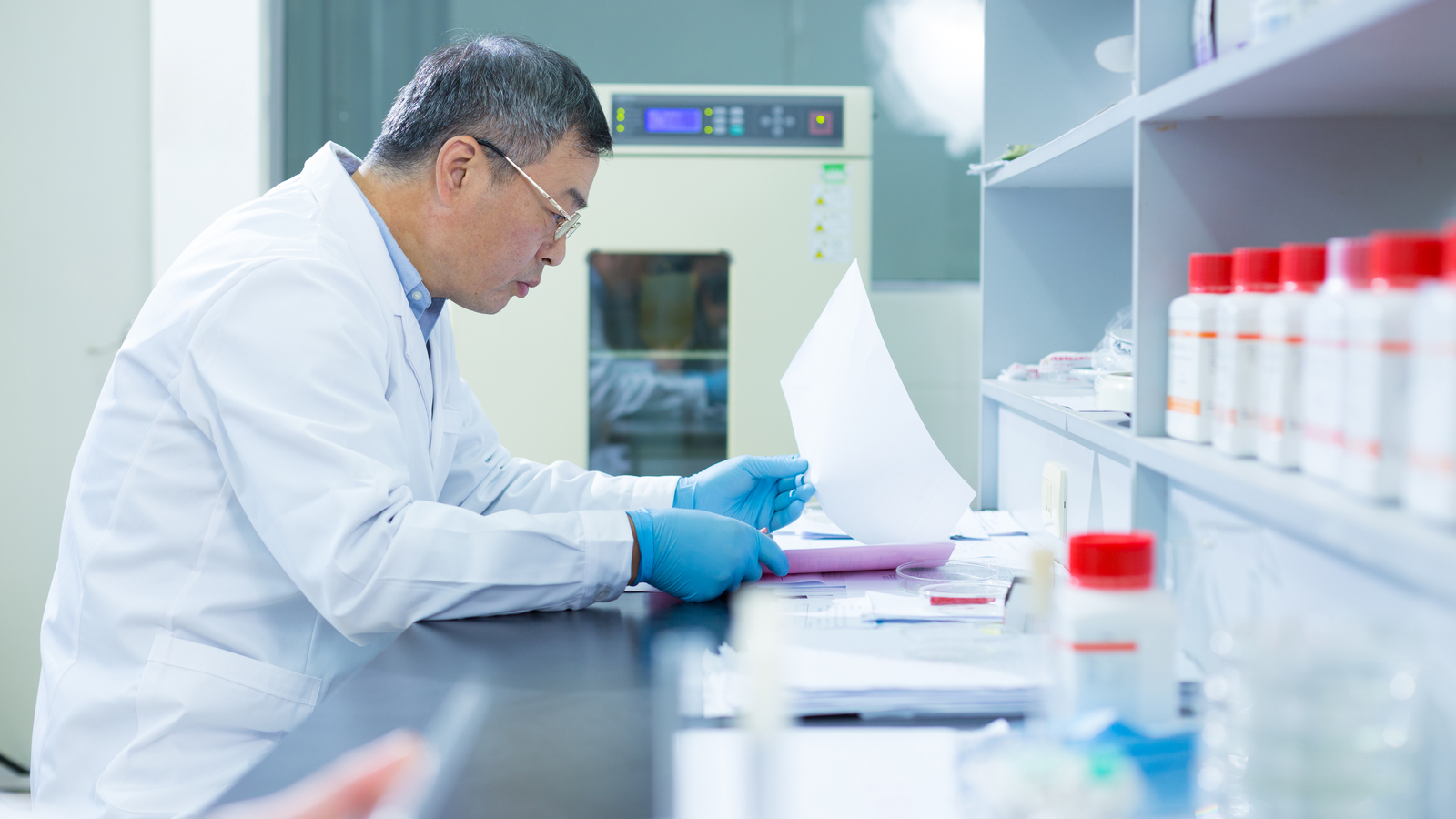