In recent years, advancements in laminated insulation material production technology have revolutionized the way energy is conserved. This breakthrough technology has enabled manufacturers to create products that are vastly more efficient than ever before, allowing for better thermal and acoustic performance.
With this new capability, architects and engineers now have access to a range of versatile options when designing their structures. The combination of improved insulation properties and efficiency enables designers to use thinner layers with greater effectiveness while reducing overall materials costs. As a result, these developments represent a major step forward in terms of sustainability as well as financial savings.
Enhanced Durability of Laminated Insulation Materials
The advancements in laminated insulation material production technology have enabled immense improvements to the durability of these materials. The combination of multiple layers of different types of insulation, such as polyurethane foam and aluminum foil, creates a strong barrier that is resistant to damage from weather or wears and tear. This layer-by-layer construction technique provides superior protection against water vapor, heat loss, and other elements that can negatively affect performance over time.
Manufacturers are now able to produce laminate insulation with enhanced durability that will last for years without any degradation in performance. Additionally, the use of durable adhesives ensures a secure bond between each layer so they won’t separate even under extreme conditions. As a result, this technology has made it possible for people to enjoy more comfortable living spaces with increased energy efficiency for longer periods.
Automation of Laminated Insulation Material Production
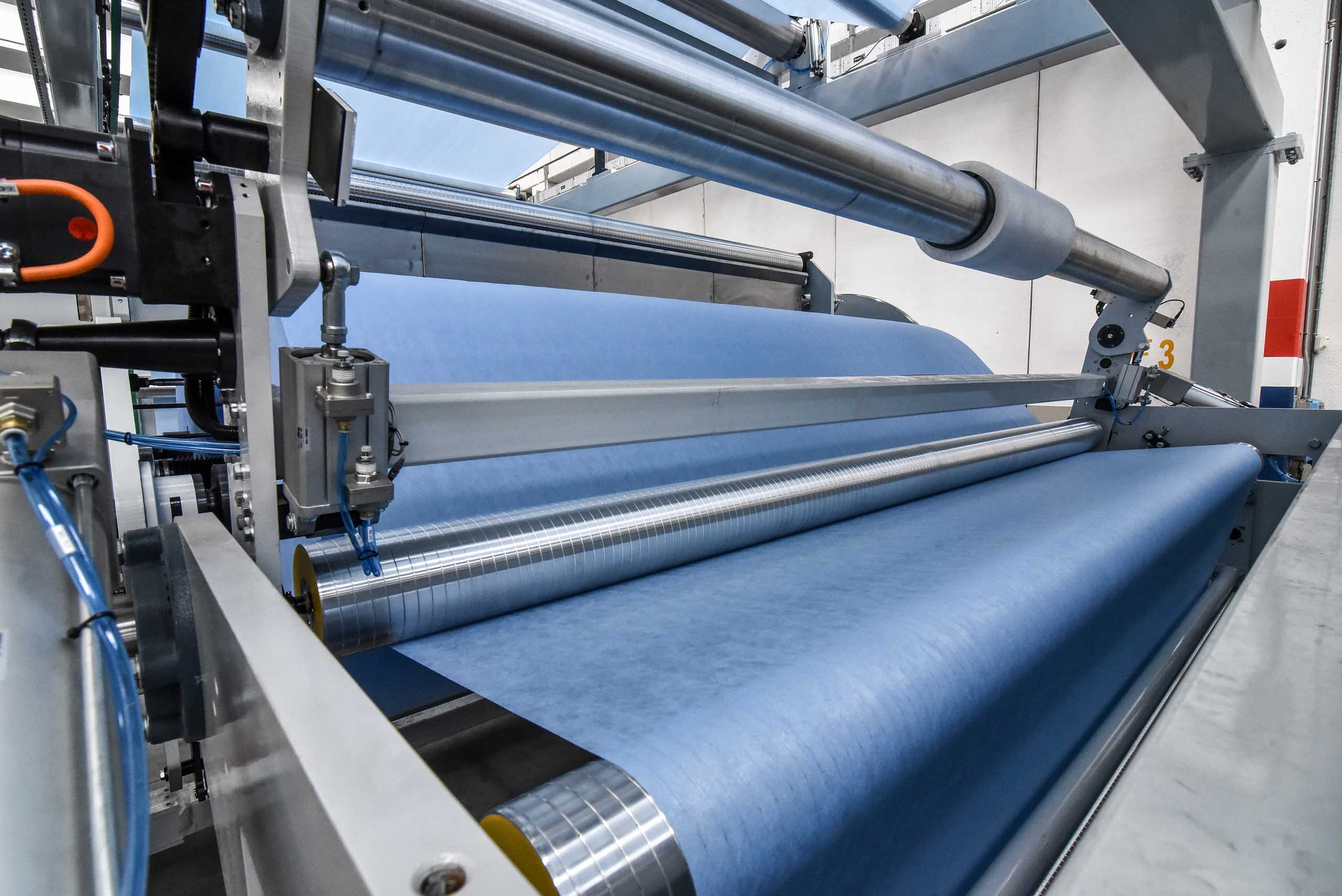
The automation of laminated insulation material production has revolutionized the industry. By introducing digital technologies such as robotics, machine learning, and automated inspection systems, manufacturers can increase productivity, reduce costs and improve product quality. Automated processes also enable faster throughput times and improved consistency in production lines. This type of technology is becoming increasingly necessary for companies to remain competitive in an ever-changing market.
Robots can operate with great precision and accuracy at high speeds while performing a wide variety of tasks within the manufacturing process. Automation also eliminates potential human errors that may occur during manual operation, ensuring consistent results every time. In addition to these benefits, it reduces labor costs by removing the need for physical labor in certain operations or functions thus increasing efficiency overall. Machine learning enables advanced analytics that can be used to detect abnormalities or inconsistencies within production lines before they become costly issues down the line.
It can provide valuable insights into areas where improvements could be made which further increases efficiency and cost savings for businesses utilizing laminated insulation materials in their products or services. Additionally, automated inspection systems allow manufacturers to quickly identify any problems that arise during production so they can address them promptly without disrupting workflow or delaying deliveries – resulting in improved customer service levels overall.
Ultimately, automation of laminated insulation material production provides numerous advantages over traditional methods – including increased productivity rates coupled with reduced operating costs; greater quality assurance; more efficient use of resources; better utilization of existing capacity; enhanced safety standards; faster turnaround times on orders & delivery schedules—all leading to higher customer satisfaction ratings too!
Adoption of Green Manufacturing in the Production of Laminated Insulation Materials
The adoption of green manufacturing techniques in the production of laminated insulation materials has become increasingly popular in recent years. Companies are recognizing that eco-friendly production processes not only benefit their bottom line but also help to preserve the environment. By using more sustainable resources and reducing energy consumption during production, organizations can reduce their carbon footprint and lessen the impact on our planet.
In addition to being a more environmentally friendly option, green manufacturing processes have been found to improve product quality and increase efficiency. Through renewable energy sources such as solar power or wind turbines, companies can achieve higher levels of productivity while still maintaining sustainability goals. Furthermore, with advances in technology over the past decade, new technologies have been developed that allow for improved control over temperature regulation and other aspects of the production process which helps optimize quality standards without sacrificing environmental considerations.
Ultimately, by incorporating green manufacturing into its operations an organization can create products that meet industry standards while also taking steps toward preserving natural resources for future generations. For these reasons, many businesses are turning towards this type of technology when it comes to producing laminated insulation materials – ensuring they produce consistently high-quality items with minimal environmental impact.
Optimization Strategies for Enhancing Quality and Efficiency in the Production of Laminated Insulation Materials
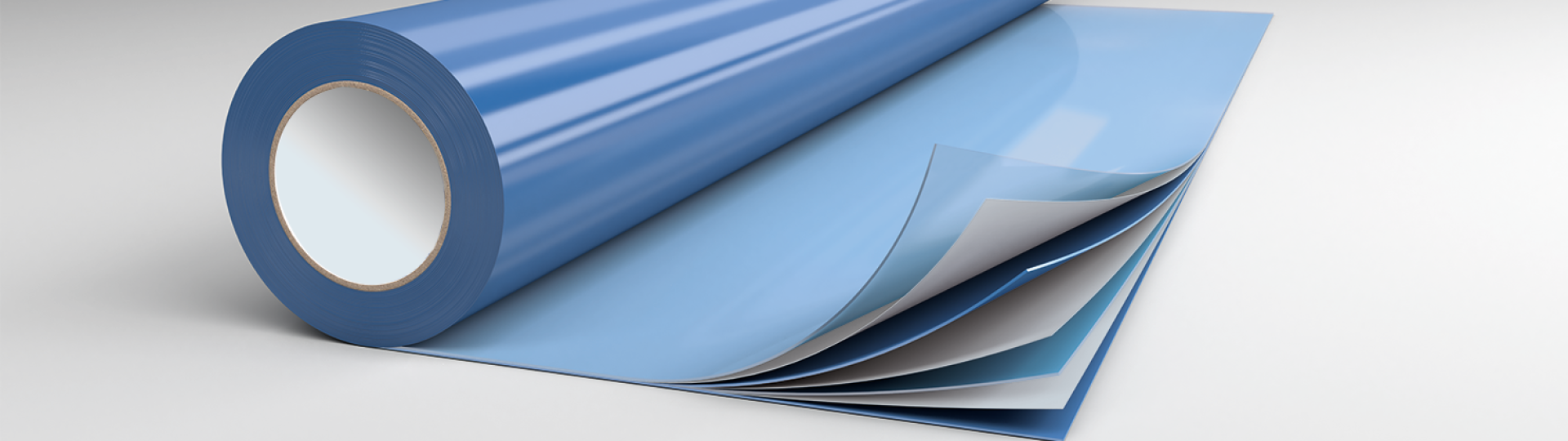
The production of laminated insulation materials has seen significant advancements in technology over the years. These improvements have resulted in the ability to enhance both quality and efficiency while creating these materials. Optimization strategies are a key factor when it comes to maximizing production capabilities and ensuring top-tier results. One of the primary optimization strategies that producers should employ is using automated processes for certain steps in the production process. Automation can help reduce errors, increase consistency, and provide greater accuracy overall. Additionally, utilizing robotics or other machinery for material handling can help minimize human labor costs associated with completing tasks like mixing ingredients or loading equipment with raw materials.
Another way to optimize quality assurance measures is by investing in updated testing procedures before shipping out products from their facilities. This could include implementing new technologies such as infrared spectroscopy or gas chromatography for determining the chemical composition of batches as well as visual inspection systems like HD cameras for detecting any defects within product samples before they reach customers. Utilizing these kinds of technologies allow manufacturers to detect problems sooner rather than later which would ultimately save them time and money on reworks or repairs down the line. Finally, companies should also consider revamping their record-keeping practices by incorporating fully digital processes into their operations management system (OMS).
Having a clear understanding of what resources were used during each stage of production will enable producers to track trends over time when it comes to cost savings and/or areas that need improvement upon delivery completion rates etc., allowing them to make more informed decisions about how best allocate funds towards specific parts/components moving forward. Overall, there are many optimization strategies available today designed specifically for enhancing quality & efficiency while producing laminated insulation materials including automation & updated testing procedures along with adopting digital record-keeping practices through OMS platforms – all geared towards saving time & money while still providing superior end products.