Car manufacturing requires precision and accuracy in the fabrication of components, which is why press brakes are essential tools for the industry. They can produce a wide variety of car parts, from bumpers to chassis.
Press brakes are used to bend metal into shapes with high accuracy, enabling manufacturers to create complex components quickly and efficiently. This article will explore the versatility of press brakes in car component production and discuss how these tools have revolutionized modern car manufacturing.
It will also examine why they are so important for producing accurate parts that meet safety standards. Finally, it will look at how this technology has opened up new possibilities for automotive design and performance improvements over time.
With their versatile capabilities and precise results, press brakes allow manufacturers to fabricate complex components with confidence – unlocking a world of possibilities in vehicle design and performance engineering.
Benefits of Using a Press Brake for Car Components
Press brakes allow car component manufacturers to shape metal parts into desired shapes with precision and consistency. The use of press brake technology in car component production offers several distinct advantages, including increased accuracy and speed, reduced material waste, improved safety standards for workers on the assembly line, and enhanced quality control over finished components.
Accuracy is critical when manufacturing car components; even small errors can lead to faulty parts that may cause serious issues down the road. With a press brake machine, manufacturers can produce highly precise bends without sacrificing any performance or durability qualities.
This means better-fitting components with fewer defects due to incorrect measurements or misalignments during production. Speed is also an important factor for efficient production lines.
Press brakes are capable of producing large quantities of identical components quickly and accurately while using less energy than traditional methods such as hand bending or hammering metal into place. This makes it possible for factories to keep up with demand while minimizing labor costs associated with slower processes like manual fabrication methods require more time and effort from employees on the assembly line. Another benefit of press brake machines is their ability to reduce material waste during manufacturing operations by allowing operators more control over how much material is used in each part being produced.
By reducing unused scrap materials generated during production runs, companies can save money by not having to buy additional raw materials or dispose of excess stock at disposal facilities which often incur additional costs associated with them – thus helping increase overall profitability margins within their businesses. Finally, investing in a press brake helps improve workplace safety standards as well as product quality due to its automated nature: since all tasks controlled by this technology are done automatically there’s less risk of injury compared human operated tools like hammers which need manual operation – plus operators don’t worry about inconsistencies between one product batch another thanks its consistent results every time!
Design Considerations When Utilizing a Press Brake
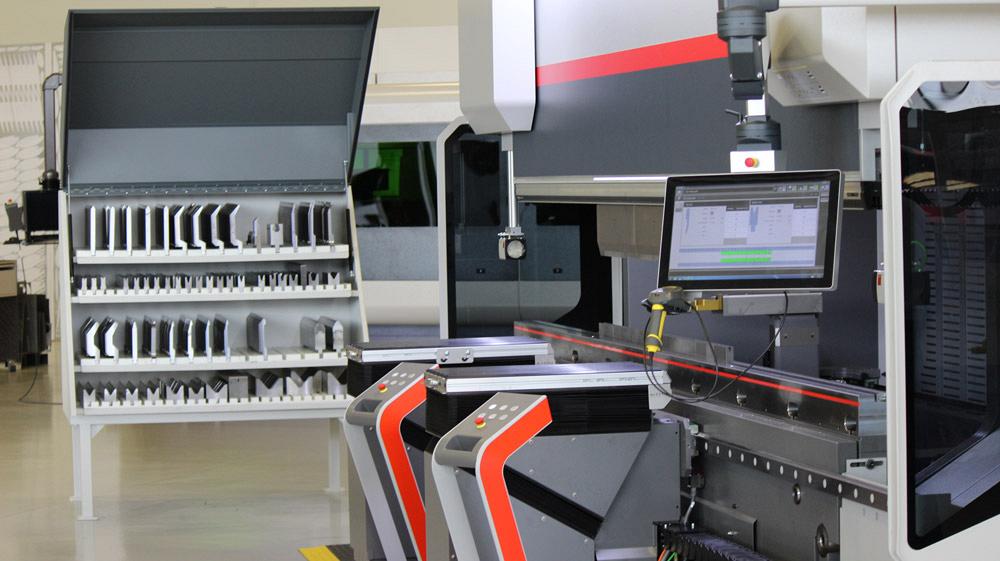
When utilizing a press brake in car component manufacturing, there are saeveral design considerations to take into account. First and foremost is the material being used; different materials require different settings on the press brakes to achieve an optimal result.
To ensure accurate and consistent results, all materials entering the machine must be of uniform thickness. Secondly, safety must be taken into consideration when operating a press brake; ensuring that all personnel involved have been trained properly will help avoid any accidents or mishaps.
Finally, tooling must also be considered when using a press brake for car components – different tools can produce very different shapes and sizes depending on their geometry and size relative to the material being formed. With these design considerations in mind, manufacturers can use a press brake for creating parts ranging from bumpers to chassis with reliable accuracy and precision.
Essential Safety Measures When Working With A Press Brake
Working with press brakes requires essential safety measures to be taken to mitigate risk. In the realm of car component manufacturing, press brakes can provide a high level of accuracy and versatility when forming components such as bumpers and chassis frames.
While the advantages may be alluring, operators need to take necessary steps to protect themselves from potentially hazardous situations that may arise due to improper usage or maintenance. Before beginning work with a press brake, workers should ensure that guards are present on all moving parts and are properly secured.
Additionally, any broken guard components should be replaced immediately before operating the machine. Operators should also check if there are any loose bolts or other pieces that could cause sudden movement during operation.
Furthermore, workers must wear appropriate protective gear such as gloves and face shields whilst using a press brake. It is also important for operators to become familiar with emergency stop buttons located on the machine itself; these allow users to quickly halt operations in case of an unexpected occurrence or danger signal without having to manually switch off power supply sources which may require more time than needed in certain cases.
Workers should practice safe lifting techniques when handling heavy objects around the machinery workspace area too; this will prevent unnecessary injuries resulting from incorrect posture while shifting items around the workplace environment. Finally, proper training regarding the operation and maintenance of press brakes must always be given prior to use so that risks associated with incorrect use can be minimized accordingly
Conclusion
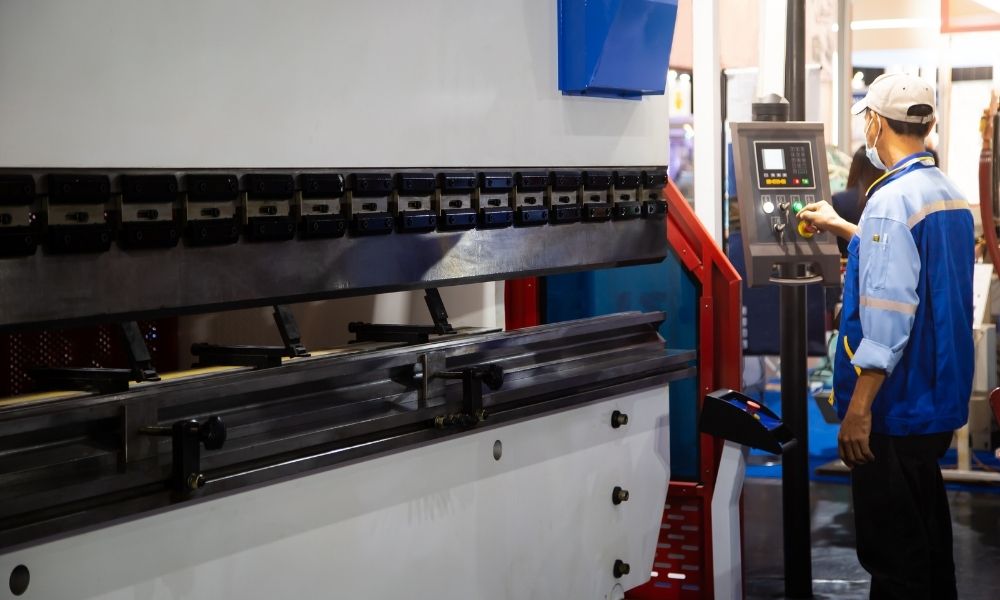
The versatility of press brakes in car component manufacturing is undeniable. From the design and fabrication of bumpers to their use in strengthening chassis components, press brakes have allowed manufacturers to produce high-quality parts with accuracy and precision.
The hydraulic press brake has become an integral part of the automotive industry, allowing for greater control over metalwork processes while increasing efficiency. With their ability to shape a wide range of materials into complex shapes, it is no surprise that press brakes are used throughout automobile production today.