The utility of PCB is directly correlated to the breadth of electrical devices and utilities found within our society nowadays. With that, production of them becomes higher in demand. However, not everybody needs an extravagant amount of PCBs in a single batch. Some people need simple, small batches. This is why a frequent question that arises ends up being: Do you handle small-batch PCB production orders.
What are PCBs?
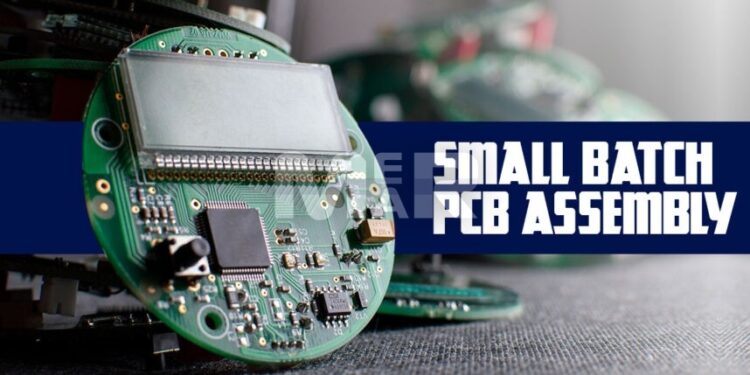
Let’s quickly go over what PCBs are and their utility. A PCB is short for printed circuit board, which is a laminated sandwich structure with different layers. These layers are conductive or insulating.
When it comes to the function of PCBs, there are two inherent functions they possess. The two are complementary, supporting each other in their functions. These would be the functionality of affixing electronic components and providing reliable electrical connections.
These functionalities work in tandem to provide support to electronic components. The components themselves are soldered onto the PCB itself, immediately utilizing the affixation angle of the first functionality while also touching upon the second as they get integrated into a system.
Just about any electronic product utilizes PCBs. Meaning their presence is heavily felt throughout multiple industries. There are multiple other applications for PCB too but the electronic products are the most obvious example of its application.
Are large manufacturers incentivized to engage with small-batch PCB production?
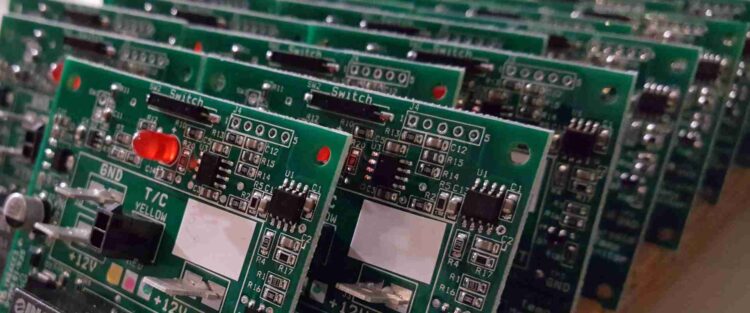
There’s an idea present within many industries that going for bigger and more elaborate products is always for the best. Engaging with something that’s less expedient in bumping up our profit seems less worth it and thus less enticing to engage in.
However, this sentiment is frequently proven wrong. It is no different with small batch PCBs. These types of operations do not have to be part of the standard operating procedure and can be given their own space within the production.
The small batch PCB assembly can benefit and utilize the more elaborate aspects of our operating procedure to maximize efficiency even further. Manufacturers such as pcbasic.com are very direct and apparent examples of this.
Benefits of handling small-batch PCB production
If we do decide to handle small batches of PCBs it would make sense to know why. If there is no benefit or incentive to do so then we’ll find ourselves without a reason to engage in something like this.
The most visible benefit is that you’ll need a lot less time to produce each batch. Considering each batch will be a lot smaller, the job will progress much faster. It’s obvious to anybody but it should be specifically noted. That also pulls with itself the benefit of having an easier time following up on the existing orders and making new ones. Without that, we’d get stuck on larger ones.
It will save us time on checking for defects. Small batch PCB production has a much easier time reviewing each board and making sure it operates well. The malfunctions and reject boards will be easily picked out from the bunch, while also being easier to replace within a batch. Checking, removing, and adding PCBs becomes much less of a hassle when there aren’t that many items in circulation.
The lower number of PCBs that are given more attention will ultimately result in a better product. The benefit of direct interaction with each board, due to some more expensive yet fast solutions being unnecessary for the process, is that extra polish can be given to PCBs.
What does it mean to handle small-batch PCB production?
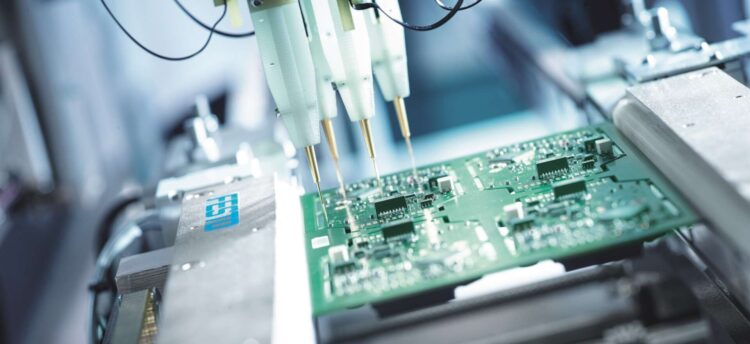
Now that we know the advantages along with the application of PCB, let’s see how the handling of their assembly proceeds. Getting a bit of insight is always good when it comes to design and production processes.
Firstly, you’ll need a design and layout for your PCB. These are paramount to a successful item. Each PCB can be configured to the needs of the client. Usually, the actual specifications will be granted by the client allowing us to focus on actually putting the blueprint into practice. The ability to exchange these blueprints easily means little time is spent before the rest of the work begins.
The next step is assembling the PCB itself. As we’ve said, smaller batches don’t require elaborate machinery nor any special specifications to conform to. It’s worthwhile to enable ourselves extra time when assembling these due to the aforementioned increase in quality. However, even that extra time won’t affect the speed much, only slightly increasing the duration of each item’s creation while giving a huge uptick in quality.
The PCBs can then be tested properly, to assure all design details have been followed up on. If there are changes to be made, they will probably be made now. Switching around potential points where the components will get soldered to as well as going through basic troubleshooting is bound to increase customer satisfaction.
Lastly, it’s fruitful to have expedient and safe shipment if you are willing to provide delivery. Potential damage to the PCBs along the way should be brought down to a minimum. This is the one area that can heavily impact the benefits mentioned above, lowering the overall utility by a bunch.
Conclusion
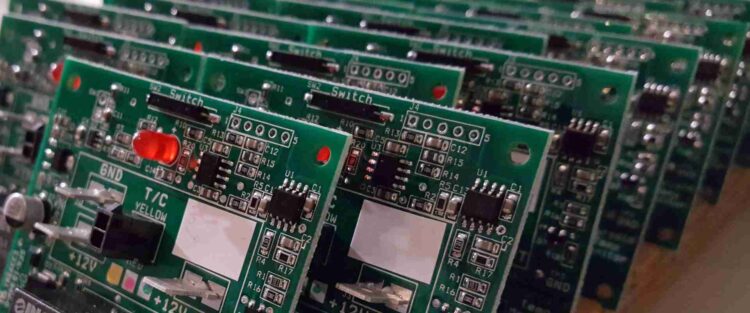
The PCB is widely used and as such has a lot of demands of all shapes and sizes. The sizes of batches are one number we should give extra attention to. For any manufacturer, engaging in small batch production could be a good way to go about their work.
This style of production brings with it many benefits like faster assembly times, better quality products, and switching from one batch to another swiftly. The speed is key here and handling the entire process by yourself could also be easily doable with little extra engagement.
Making the PCB then remains the last step before a finished product can be safely shipped. With the benefits provided and the manufacturing process followed up on, we should have a fruitful production with few issues.