Thermal shock chambers provide a unique way to test the durability of materials in extreme temperatures and environments. They are used by scientists, engineers, and manufacturers to evaluate how well components or items will respond when exposed to rapid temperature changes.
This comprehensive guide outlines the purposes of thermal shock chambers and explains their usage in detail so that you can make an informed decision about which type is best for your needs.
It also covers topics such as safety considerations, setup requirements, maintenance tips, and more – all designed to help you get the most out of your thermal shock chamber experience. So whether you’re looking for a reliable testing solution or just curious about what these machines can do – this guide has you covered!
Types of Thermal Shock Chambers and Their Applications

Thermal shock chambers are used to simulate extreme temperature changes and environmental conditions. They come in several types, each with its unique application.
One type of thermal shock chamber is the mechanical thermal shock chamber which uses a mechanical system to generate rapid temperature fluctuations from below-freezing temperatures to above-ambient temperatures.
This type of thermal shock chamber can be utilized for testing materials’ resistance to sudden temperature change or accelerated aging tests. Another type of thermal shock chamber is the pneumatic thermal shock chamber which uses heated air instead of a mechanical system for rapid temperature changes.
It has applications such as stress relief annealing, solder joint fatigue testing, and corrosion resistance testing on metal components at elevated temperatures over long periods. Finally, liquid nitrogen-based cryogenic freezers are another type of thermal shock chamber that offers subzero temperatures for extremely fast cooling rates when used properly in combination with other test parameters such as humidity and pressure levels.
These chambers can be used to perform impact tests at low temperatures or even cold storage tests on food products or pharmaceuticals before they reach the market shelves
Evaluation Criteria for Choosing the Right Thermal Shock Chamber

When evaluating the right thermal shock chamber, there are several essential criteria to consider. First and foremost, it is important to check the range of temperature variation that can be achieved in each cycle and how quickly the temperatures change between high and low extremes.
Additionally, assess whether or not additional options such as humidity control and forced air circulation are necessary for your testing needs. Noise levels should also be evaluated; some chambers produce higher noise levels than others so this must be taken into account when deciding on a model.
Furthermore, many models come with safety features that provide vital protection against unexpected events during operation, making sure that personnel will remain safe while using the chamber. Finally, reliability is key when selecting a thermal shock chamber; make sure to read reviews from other users who have used the same model before purchasing one yourself.
By considering all these factors you can ensure that you choose the best thermal shock chamber for your needs.
Operating Procedures for Thermal Shock Chambers
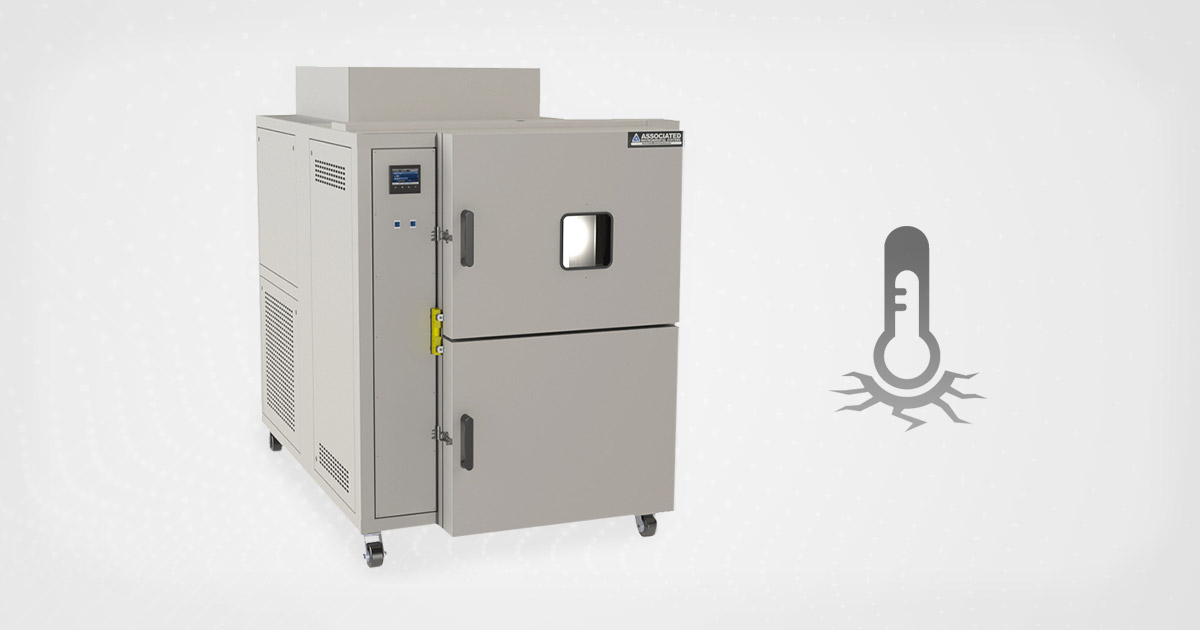
When operating a thermal shock chamber, it is important to understand the safety procedures associated with its use. All personnel must be adequately trained in the proper handling and operation of this equipment before beginning any tests.
Additionally, protective clothing should always be worn while conducting experiments inside the chamber as temperatures can rapidly fluctuate between extreme highs and lows. Furthermore, all electrical components should be checked for proper connections and insulation before each usage session.
Emergency shut-off switches should also be utilized during testing to protect people and equipment from unexpected events or malfunctions that may occur unexpectedly during experimentation cycles. Finally, regular maintenance such as temperature calibration checks, lubrication of moving parts, cleaning out lint/dirt build-up within the unit, and servicing at least once every two years are necessary steps for ensuring optimal performance from your thermal shock chamber over time.
Safety Considerations When Working with a Thermal Shock Chamber
Safety is a key consideration when working with thermal shock chambers. Before beginning any tests, it’s important to ensure that the chamber is properly grounded and protected against electrical hazards.
Additionally, all personnel involved must be trained in proper safety protocols for handling hazardous materials and operating the equipment. Protective clothing should also be worn at all times while conducting tests within the chamber.
It’s essential to take necessary precautions such as using insulated gloves or taking regular breaks to avoid overexposure to extreme temperatures inside the chamber. Furthermore, emergency shut-off switches and other safety features should always be used during testing procedures for added protection of people and equipment alike.
Finally, regular maintenance of the thermal shock chamber is recommended to keep it running efficiently while minimizing potential risks associated with its use.
Maintenance Requirements for Proper Performance of a Thermal Shock Chamber
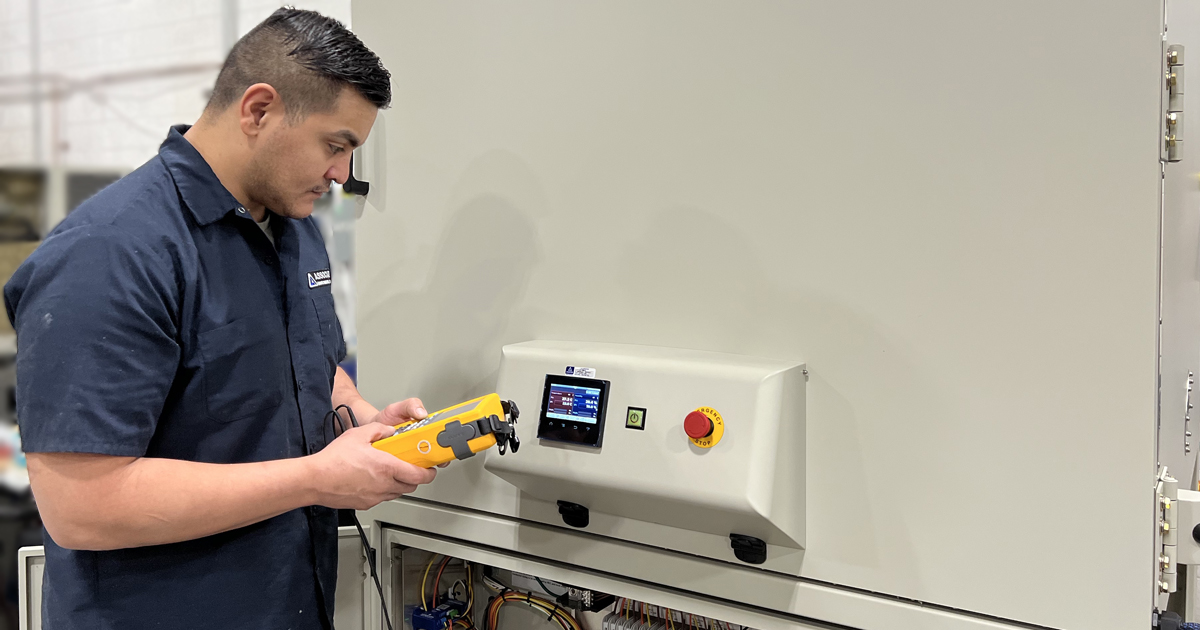
When it comes to maintaining a thermal shock chamber, several important steps must be taken to ensure proper performance. Regularly checking the temperature accuracy and calibration of the temperature control system is an absolute necessity for any thermal shock chamber.
Additionally, ensuring all components remain properly lubricated can help prevent wear and tear on components as well as improve their overall efficiency. It’s also essential to keep all seals and gaskets in good condition, so they don’t break down or become damaged during use.
Furthermore, cleaning out any lint or dirt from inside the chamber can help maintain its integrity by preventing corrosion from forming inside the unit. Finally, servicing should always be done according to manufacturer guidelines at least once every two years to guarantee excellent performance over time.
Conclusion
A thermal shock chamber is an invaluable tool in the testing and evaluation of materials. Its ability to rapidly cycle between extreme temperatures makes it ideal for many applications, including research on material properties, product testing, failure analysis, stress relief, and more.
Using a thermal shock chamber can help ensure that components can withstand the rigorous environmental conditions they may encounter in their intended use scenarios.
With its wide array of uses and numerous benefits, a thermal shock chamber is an essential piece of equipment for any laboratory or industrial setting looking to test products under extreme temperature changes.