Efficiency in motion: mastering the art of rotary screw air compressors is a journey into the world of cutting-edge technology and industrial engineering. From its origins as a simple tool for powering pneumatic tools to its current use in countless industries around the world, this guide will explore all aspects of rotary screw air compressors and how they can be used to achieve maximum efficiency.
Along the way, readers will learn about their inner workings, discover innovative ways to optimize them for specific applications, and understand how they can become an indispensable part of any successful business or manufacturing operation. So join us on this journey into understanding one of the most important technological advancements in modern times – rotary screw air compressors!
Understanding the Basics of Rotary Screw Air Compressors
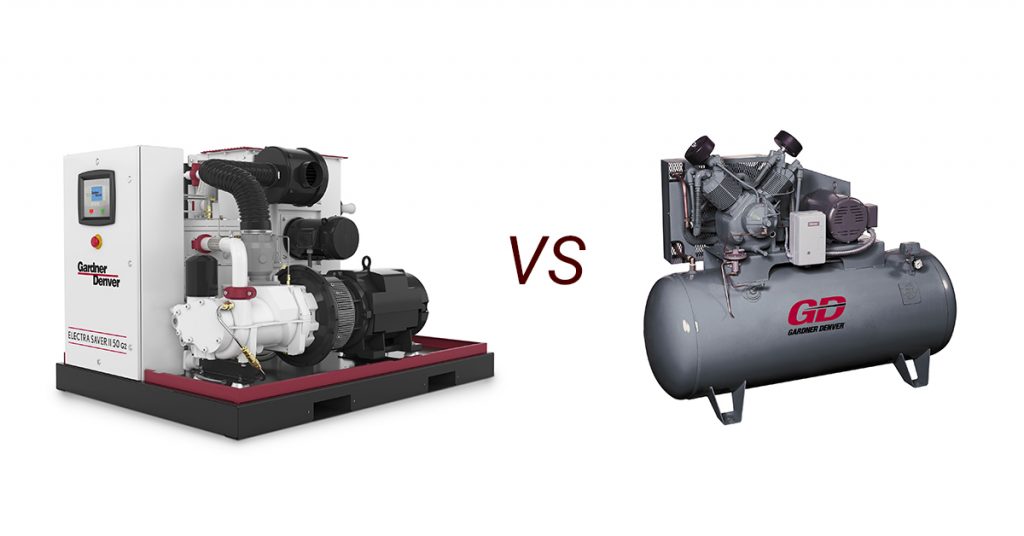
Rotary Screw Air Compressors are an efficient and reliable method of delivering compressed air to industrial applications. They offer a variety of advantages over other types of compressors, such as increased energy efficiency, lower costs, and less maintenance. Understanding the basics behind rotary screw air compressors is essential for anyone looking to make the most out of these machines.
To maximize efficiency, it is important to understand how these machines work. A rotary screw compressor uses two counter-rotating screws which rotate in opposite directions at different speeds to generate compression within the housing chamber.
This creates higher pressures than traditional reciprocating piston-type compressors while keeping temperatures low and providing greater reliability due to fewer moving parts.
Maximizing Efficiency in Your Compressor System

Maximizing efficiency in your compressor system is key to mastering the art of rotary screw air compressors. There are several ways to ensure that you’re getting the most out of your equipment and keeping up with industry standards.
Regular maintenance, proper calibration, and careful monitoring can all go a long way toward achieving greater levels of efficiency while ensuring maximum uptime for your compressor system. It’s also important to invest in quality components so that you have access to reliable parts when needed.
Additionally, make sure that filters are regularly changed and inspected as part of routine maintenance practices – this will help maintain healthy pressure levels throughout the system. Finally, don’t overlook the importance of workforce training; investing time into educating staff members on safety protocols and preventive maintenance tasks can pay dividends down the line by helping them identify potential problems before they arise.
By following these simple steps, it’s possible to maximize efficiency in even the most complex compressor systems while staying ahead of competitors in an ever-evolving manufacturing landscape.
Proper Maintenance for Optimal Performance
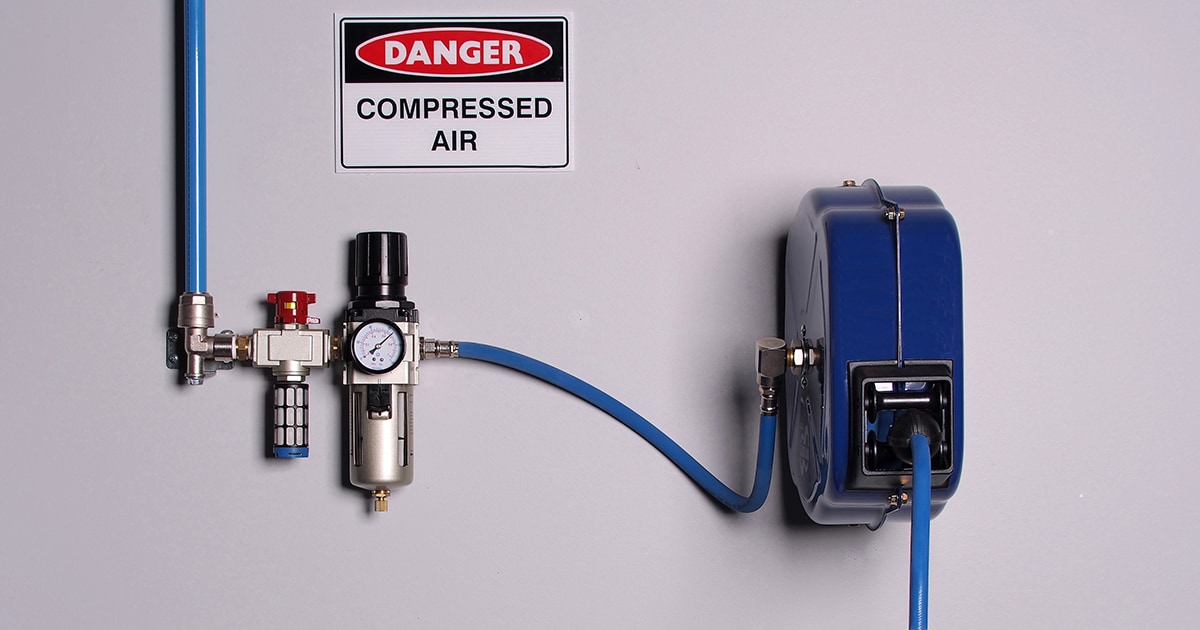
Proper maintenance for optimal performance of rotary screw air compressors is essential to ensure maximum efficiency in motion. Regular inspections should be conducted to check the condition of internal components and lubricants, as well as any external connections or hoses.
During these inspections, all signs of wear and tear must be monitored closely, as they can indicate underlying issues that could compromise the performance of the system. Additionally, filters should also be checked regularly and replaced if necessary to maintain optimum air quality levels within the compressor.
Finally, routine check-ups with a qualified technician can help detect potential problems before they become serious enough to cause costly damage or downtime. By taking the necessary steps to keep your rotary screw air compressor functioning at its peak capacity, you can ensure reliable operation over time with minimal disruption.
Conclusion
In conclusion, Rotary Screw Air Compressors have revolutionized the efficiency of air compression. By utilizing cutting-edge technology and unparalleled engineering, these compressors can provide a reliable and cost-effective solution for industrial applications.
With their unmatched abilities in energy savings and longevity, they are quickly becoming one of the preferred choices for businesses looking to optimize production capabilities while minimizing operating costs.