Have you ever wondered how some small metal parts found in electronic appliances are made? I keep asking myself this question because sometimes it seems incredibly difficult to produce these parts. Are machines used or do workers make the parts by hand? In the manufacturing industry, to produce certain products that contain metal components, until recently, laser machines for cutting metal pieces were used to obtain the required dimensions or water presses that were also intended for this purpose. However, in such processes, the metal pieces, depending on the material, can be damaged, bent, or have a lot of unevenness. But today there is a solution to this problem, and that solution is called photo etching.
For all of you who are part of the engineering industry and want to learn more about this process, stay tuned as we have prepared a lot of tips and guidelines involved in this process. But above all, let’s start with the introduction of the term and what it means.
What is photo etching?
You will find this process in the industry under various names, the original being photo etching, and the terms metal etching, acid etching, photo chemical etching, and many other names are also used. We must mention that this industry has become extremely popular and widely used in the last year. This process involves the production of complex and small metal components for the needs of other industries, such as medical, automotive, military, electronics, and so on. These sectors use appliances and items that contain small metal components that are very difficult to make, so these industries opt for the photo etching method which is much cheaper and more accurate than any other.
The goal of the engineers is to find the ideal process for designing these small and specific pieces, and this process begins with their design. Here are some tips for photo etching design that all engineers must follow in their work.
-
The choice of metals
First of all, to start this process, you must know the metals you will be working with. Metal etching methods use the most diverse types of metals, such as aluminum, copper, steel and stainless steel, nickel, and many other metals. In other processes, such as printing or laser cutting, sudden damage to both the machine and the parts themselves can occur when molding parts. For example, in many cases, laser cutting of aluminum is avoided because in this activity the aluminum gives a glow that can destroy the machine. Therefore, a better alternative is photo etching, where there is no risk in creating the metal component.
-
Dimensions
As already mentioned, many industries need this service because they use it in their production and operation pieces with different dimensions and thicknesses. In this activity to make thicker metal parts, the process of making them would take a little longer and would be a little more expensive than the smaller ones. While for thinner and more complicated metal components, the photo etching process is significantly shorter in time and cheaper. For this mission to be successful, the engineer must pay attention to the dimensions from the very beginning, because if something goes wrong, the whole activity must start from the very beginning.
-
Cleanliness in the first place
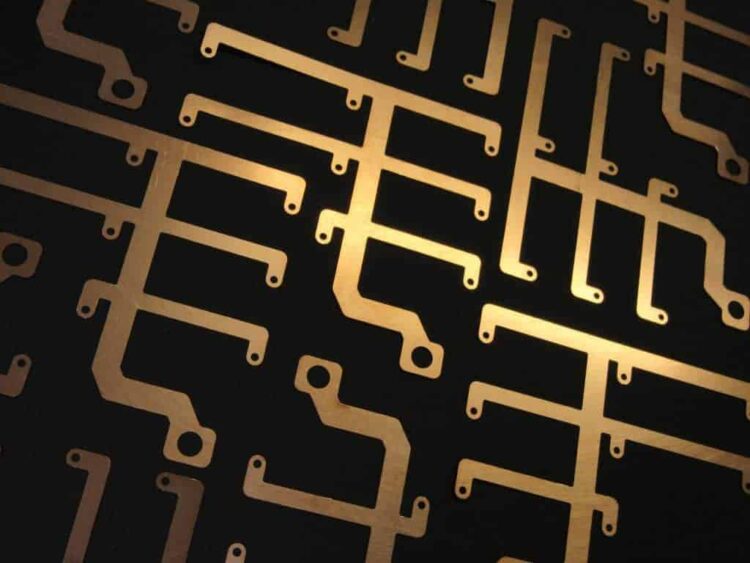
As part of the design process is cleaning the sheet we work with. You must be extremely careful about this step and any metal plate must be clean before the etching process. Once this phase is complete the next thing to do is spray the plate with acid. Acid spraying is applied in a vertical direction. This application of acid allows us to further manipulate the design of the metal sheet, the edges can be tilted, recesses and bumps can be made, and so on.
-
Half etched parts
If a company or manufacturing plant needs semi-etched components, this can be accomplished in the metal etching process. Usually, some consumers demand such metal parts which can be further finished by hand. Further manual molding of metal parts would save the company money on machine molding, and there is no chance of making a mistake if it were done manually.
-
No need to rush
In the design and metal etching process, the most important thing and advice that you should follow if you want to be successful is of course not to rush. When we rush into doing a task, we will likely make a mistake that will further produce additional complications, so we will have to start all over again. Starting a design from scratch involves additional uses of cost-effective work resources. And not only that, why not repeat the whole cost and process when you can master it from the first try. Only with enough concentration and focus on what you do without any pressure will you be able to complete this task on time and professionally.
The photochemical etching itself brings many positive features to the industries, and some of those advantages are lower costs for the production of metal components, lower chances for inequality or inadequacy of metal parts, creating perfect copies of complex components, and so on. These are just a few of the positives that would make a company opt for metal etching instead of laser or stamping.
Here we end at the very end of this article that was intended for you. In it, we presented some tips related to the design itself in the activity called photo etching, and how to improve it. As an engineer, you need to strive to be the best at what you do and leave your clients satisfied with what you do. By following this guide, you will succeed in this goal. For the very end, we can only suggest, if you have any ambiguity on this topic, to visit the link above where in detail you will find information about everything that interests you about this topic.
Just think how fast technology is advancing, who would have thought that there would be an easier, faster, and more effective way to create pieces that fit into a computer, car, electronics, etc. Who knows what else awaits us in the future and how much the technology sector could develop, we just have to wait for that to happen.